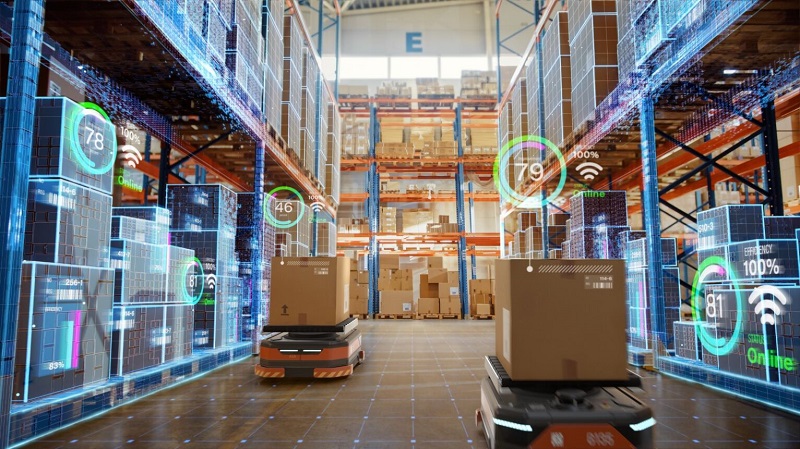
Three Good Reasons for Cold Stores to Use WMS
Cold chain warehouse operators have long understood the benefits of warehouse management software (WMS). Increases in accuracy and efficiency were often enough to justify the effort and investment required in the past. But the cold chain is becoming more sophisticated and complex, requiring closer interaction with supply chain partners, compliance with even more and stricter regulation, and the ever-present need to deliver innovation to remain competitive. There may be more good reasons why cold chain partners should consider the potential for the latest warehouse management software to support these objectives and more.
Optimising Space: making better use of available space can defer or eliminate the need for potentially expensive extensions or new buildings. This is one of the core benefits of any WMS but modern systems go much further than their predecessors. They are extremely good at managing day-to-day storage and handling operations so that all available spaces are used to maximum effect. Although warehouses are still used for consolidation, holding buffer stock, and fulfilling orders, for many the emphasis has moved from basic storage efficiency to higher throughputs. In simple terms, if stock spends less time in the warehouse the overall capacity of the facility is increased, thereby removing the need for additional space. WMS can help in a number of ways. One is to introduce new forms of handling equipment, ideally in conjunction with automation of physical and logical processes, to increase capacity and throughput. Another is to enable closer collaboration with customers and suppliers they can help the business to align stock more closely with supply and demand. This can result in less stock being held which releases space for other uses or reduces the time stock spends in the warehouse. WMS reporting and analytical tools – increasingly utilising artificial intelligence (AI) and business intelligence (BI) capabilities – can identify opportunities to reconfigure storage locations for greater efficiency. C&M Cold Stores, for example, increased storage density at its 10,700m2 (115,000ft2) facility in County Monaghan, Ireland by around 70 per cent following the implementation of Principal Logistics Technologies’ ProWMS application in conjunction with automated storage and retrieval equipment systems from Moffett Automation. In addition to the increase in capacity the solution has delivered significant improvements in productivity and safety, and labour cost reductions, while supporting new and more flexible ways of working.
Inventory Visibility: like most food-related businesses, temperature-controlled facilities usually need to manage stock rotation. Managing these processes accurately and in real time using rules such as first-in, first-out or last-in, last-out is another core WMS benefit. This is routinely achieved through integration with barcode scanning, RFID and other technologies which support and enable greater levels of automation. Modern applications go further by managing a much wider range of standard and user-defined variables to enable highly flexible operations that can adapt in real-time to changing demands. For example, orders may need to be picked for same day, next day, or day one for day three delivery to meet varying customer specifications and requirements. Accurate stock visibility in conjunction with sophisticated AI and BI functions allows the WMS to prioritise stock handling and picking operations dynamically and in real time so that the maximum number of orders are fulfilled on time and in full during each shift. Enabling stock visibility to supply chain partners can strengthen partnerships and lead to innovations on both sides. For example, Magnvale deployed ProWMS at its 46,500m2 (500,000ft2) cold store in Chesterfield to support a number of service innovations. The system now interfaces with customers through EDI as well as applications such as SAPR3 and Microsoft MS Dynamics to provide seamless access. This has reduced, and often eliminated, the need to import or rekey information manually. The system also automatically incorporates each customer’s individual pre-set business rules and specific parameters such as where to place different types of product.
Food Safety and Compliance: food safety is always important and the rules and regulations covering the cold chain are becoming increasingly burdensome. Businesses routinely need to track a large number of variables associated with individual items and batches covering everything from provenance to destination, processes completed, and a detailed record of temperature history. Ornua Foods, Ireland’s largest dairy products exporter, for example, delivers around 7000 pallets a day across is extensive international network and each can be associated with up to 150 data attributes. These include details of the original production date which is critical to record but which can have varying degrees of significance depending on factors such as the food type, related regulations, the specific customer, and the market. It is essential that the business has full, real-time stock visibility for the efficiency of its own operations but there are also requirements for complete product traceability mandated by organisations such as the Food Standards Agency in the UK, the EFSA in the EU, the FDA in the US, and other global food safety authorities. Recording and tracking this volume of information without some form of IT would be near on impossible, let alone managing the general handling and storage complexities of the cold chain. Implementing ProWMS delivered this functionality to Ornua Foods in a single application that the business integrated with its ERP and other business applications. Real-time links with suppliers and distributors have reduced the need to rekey information and enhanced product traceability across the cold chain. At the same time, improvements in resolving stock queries and discrepancies mean that Ornua Foods is paid quicker and often automatically. Transport partners reported that truck turnaround times were reduced because information was available in real time and typically pre-notified before vehicles arrived on site.
These are just three examples of how cold chain warehouse operators can improve their business performance and deliver new customer services and other innovations while keeping pace with fast-changing business and market pressures. The ongoing transformation of the sector, like many others, to embrace robotics and automation and the trend towards greater use of AI and BI will require that the underlying core applications such as WMS continue to offer their traditional benefits while integrating with these new technologies and methodologies.
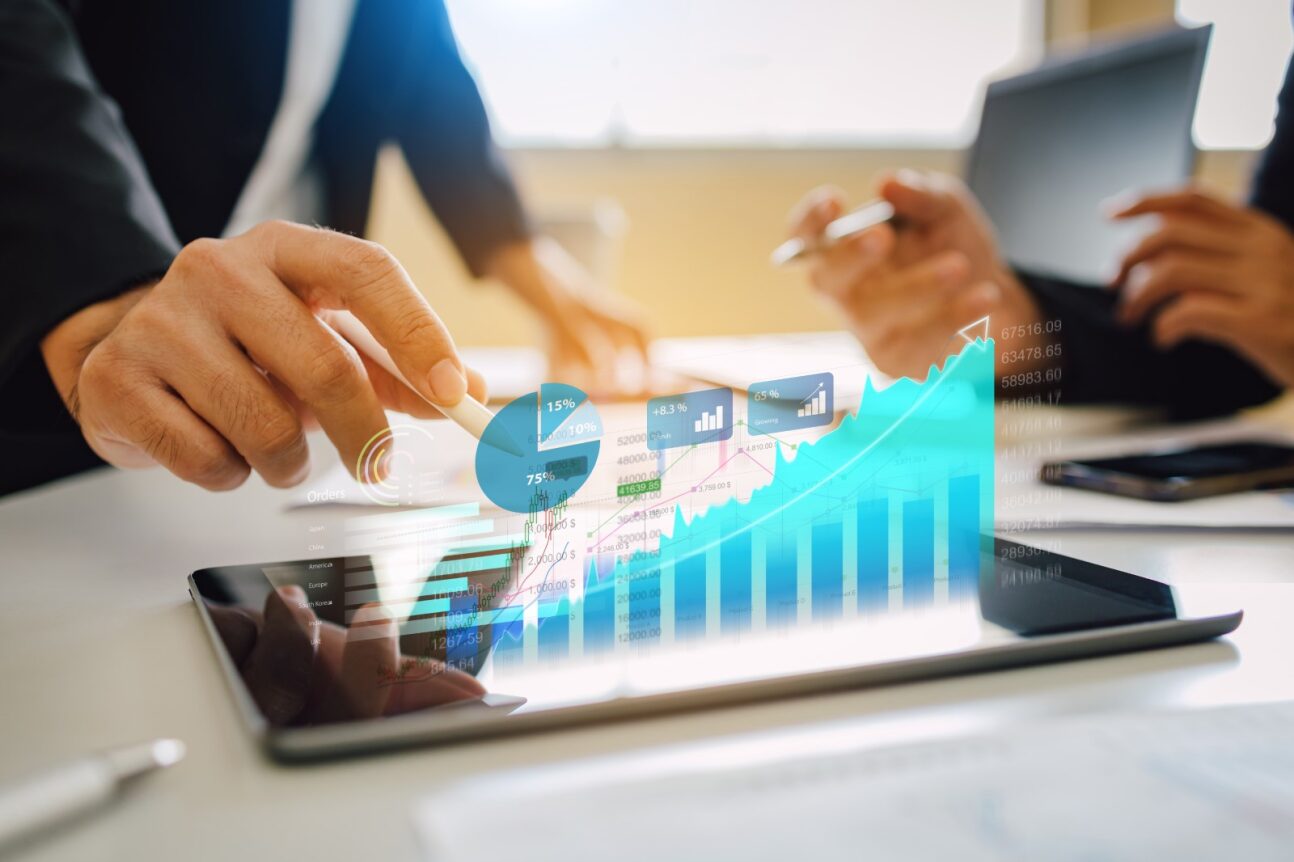
Comments are closed.